Understanding the Different Types of Butterfly Valves and Their Uses
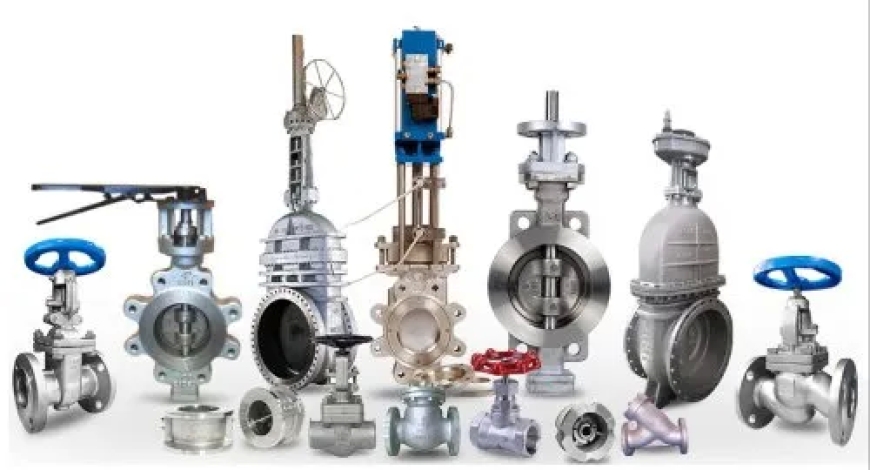
Butterfly valves are essential components in fluid control systems, providing efficient and reliable control over fluid flow in various industrial applications. Their compact design, cost-effectiveness, and ease of operation make them a popular choice across multiple sectors. This comprehensive guide explores the different types of butterfly valves, their specific uses, and the key factors to consider when selecting the right valve for your needs.
What is a Butterfly Valve?
Definition and Function
A butterfly valve is a quarter-turn rotational motion valve used to stop, regulate, and start fluid flow. It consists of a disc, body, stem, and seat. When the valve is fully closed, the disc blocks the line, and when fully open, the disc is perpendicular to the flow of fluid, allowing nearly unrestricted passage.
Advantages of Butterfly Valves
-
Compact Design and Lightweight: Butterfly valves are smaller and lighter than other types of valves, such as gate and ball valves, making them easier to install and maintain.
-
Cost-Effective: Generally, butterfly valves are less expensive than other valve types due to their simple design and fewer components.
-
Quick Operation: They offer fast operation with a 90-degree turn from fully open to fully closed.
-
Low Maintenance Requirements: With fewer moving parts, butterfly valves require less maintenance and offer long-term reliability.
Types of Butterfly Valves
Wafer Butterfly Valves
Design and Structure
Wafer butterfly valves have a thin, compact design without flanged ends. They fit between two pipe flanges and are held in place by bolts passing through the flanges and valve body.
Uses and Applications
-
Suitable for Low-Pressure Applications: Ideal for systems that do not experience high pressures.
-
Common Industries: HVAC, water treatment, food processing, and bulk fluid control system suppliers.
Lug Butterfly Valves
Design and Structure
Lug butterfly valves have a body with threaded inserts (lugs) around the circumference. They are installed using bolts that connect the valve between two flanges, allowing for one side of the piping system to be disconnected without affecting the other.
Uses and Applications
-
Frequent Maintenance or Disassembly: Suitable for systems requiring regular maintenance.
-
Common Industries: Chemical processing, wastewater management, paper mills, and valve manufacturers in India.
Flanged Butterfly Valves
Design and Structure
Flanged butterfly valves have flanged ends that are bolted to the pipe flanges. This design provides a stronger connection and better sealing capabilities.
Uses and Applications
-
High-Pressure Applications: Suitable for systems experiencing high pressures.
-
Common Industries: Oil and gas, power generation, marine industries, and butterfly valves manufacturers.
High-Performance Butterfly Valves (HPBV)
Design and Structure
High-performance butterfly valves feature a double-offset or triple-offset disc design. These designs enhance sealing capabilities and reduce wear on the seat.
Uses and Applications
-
High-Pressure and High-Temperature Applications: Ideal for environments requiring robust sealing and durability.
-
Common Industries: Power plants, refineries, and cryogenic services.
Triple Offset Butterfly Valves (TOBV)
Design and Structure
Triple offset butterfly valves have three offsets to eliminate friction between the disc and seat. They use metal-to-metal sealing for zero leakage.
Uses and Applications
-
Critical Applications Requiring Tight Shutoff: Essential for systems where leakage cannot be tolerated.
-
Common Industries: Petrochemical, LNG, aerospace industries, and ball valve manufacturers.
Resilient Seated Butterfly Valves
Design and Structure
Resilient seated butterfly valves have a rubber or elastomer-lined seat that ensures a tight seal. The flexible seat provides excellent sealing performance.
Uses and Applications
-
General-Purpose Applications: Versatile and suitable for a wide range of applications.
-
Common Industries: Water distribution, food and beverage, chemical industries, and bulk fluid control system suppliers.
Key Factors in Choosing a Butterfly Valve
Application Requirements
-
Determining the Specific Use Case and Fluid Type: Identify the fluid type (liquid, gas, slurry) and the specific use case (isolation, throttling).
-
Understanding Pressure and Temperature Conditions: Evaluate the operating pressure and temperature ranges to select a valve that can withstand these conditions.
Material Compatibility
-
Selecting the Right Materials for the Body, Disc, and Seat: Ensure that the materials used in the valve are compatible with the fluid being controlled to prevent corrosion and degradation.
-
Ensuring Compatibility with the Fluid Being Controlled: Match the valve materials to the specific chemical properties of the fluid.
Installation Environment
-
Considering the Space and Configuration of the Piping System: Assess the available space and the layout of the piping system to choose a valve that fits properly.
-
Evaluating Accessibility for Maintenance and Operation: Ensure that the valve is accessible for regular maintenance and operation without requiring significant system disassembly.
Operational Considerations
-
Manual vs. Automated Operation: Decide whether the valve will be operated manually or require automation for remote control and monitoring.
-
Actuation Methods (Electric, Pneumatic, Hydraulic): Choose the appropriate actuation method based on the system's requirements and available power sources.
Benefits of Using the Right Butterfly Valve
Enhanced System Efficiency
-
Improved Flow Control and Reduced Energy Consumption: Butterfly valves provide precise flow control, reducing energy consumption and improving system efficiency.
-
Optimal Performance in Specific Applications: Selecting the right valve type ensures optimal performance for specific industrial applications.
Cost Savings
-
Lower Initial Costs and Reduced Maintenance Expenses: Butterfly valves are generally more cost-effective than other valve types, with lower initial costs and reduced maintenance requirements.
-
Longer Lifespan and Durability: High-quality butterfly valves offer long-term reliability, minimizing the need for frequent replacements.
Safety and Reliability
-
Reliable Sealing and Reduced Risk of Leaks: Properly selected and maintained butterfly valves provide reliable sealing, reducing the risk of leaks and associated safety hazards.
-
Compliance with Industry Standards and Regulations: Using valves that meet industry standards ensures compliance with safety and operational regulations.
Case Studies and Real-World Applications
Case Study 1: Water Treatment Plant
-
Specific Challenges and Requirements: A water treatment plant needed reliable valves for low-pressure applications to manage water flow and treatment processes.
-
Selection and Implementation of Wafer Butterfly Valves: The plant selected wafer butterfly valves for their compact design and cost-effectiveness.
-
Results and Benefits Achieved: Improved flow control, reduced maintenance costs, and enhanced overall system efficiency.
Case Study 2: Chemical Processing Facility
-
Specific Challenges and Requirements: A chemical processing facility required valves that could handle high temperatures and corrosive fluids.
-
Selection and Implementation of High-Performance Butterfly Valves: High-performance butterfly valves with double-offset design were chosen for their durability and sealing capabilities.
-
Results and Benefits Achieved: Increased operational reliability, reduced downtime, and improved safety.
Case Study 3: Oil Refinery
-
Specific Challenges and Requirements: An oil refinery needed valves capable of providing zero leakage in critical applications.
-
Selection and Implementation of Triple Offset Butterfly Valves: Triple offset butterfly valves were selected for their metal-to-metal sealing and zero leakage performance.
-
Results and Benefits Achieved: Enhanced safety, compliance with industry standards, and reduced risk of environmental contamination.
Conclusion
Selecting the right butterfly valve is crucial for ensuring the efficiency, reliability, and safety of fluid control systems in various industrial applications. By understanding the different types of butterfly valves and their specific uses, businesses can make informed decisions that enhance system performance and reduce operational costs. Consulting with experts and reputable valve manufacturers in India is essential to finding the optimal solution for your specific needs.
What's Your Reaction?
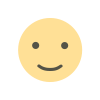

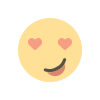

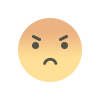

