The Importance of Melt Flow Index Testing in Polymer Manufacturing
In polymer manufacturing, the process of shaping and molding polymers into usable products requires careful control of material properties.
One key property that governs how easily a polymer can be processed is its melt flow rate, measured by a Melt Flow Index Tester. This tool is essential for evaluating how polymers behave when heated, helping manufacturers optimize their production processes and maintain high-quality standards.
At Pacorr, we understand the importance of having reliable testing equipment to ensure that polymers meet their intended performance specifications. This article explores the concept of the Melt Flow Index (MFI), why it is crucial for polymer manufacturing, and how testing with the right equipment can improve product quality and manufacturing efficiency.
What is Melt Flow Index (MFI)?
The Melt Flow Index (MFI) is a measurement used to assess the flow characteristics of a polymer when it is melted and subjected to pressure. This test helps determine the material’s viscosity, or resistance to flow, under specific temperature and pressure conditions. The MFI is determined by heating a polymer sample to its melting point, then forcing it through a die using a standard weight or pressure. The quantity of material that flows through the die in 10 minutes is recorded, and this value is expressed in grams per 10 minutes (g/10min).
A higher Melt Flow Index Testing Machine indicates a polymer with a lower viscosity, meaning it flows more easily, while a lower MFI shows that the polymer is more viscous and harder to process. The MFI value plays a crucial role in determining the suitability of a polymer for different manufacturing applications.
Why is MFI Testing Important?
- Predicting Material Behavior
Knowing the MFI value of a polymer gives manufacturers insight into how the material will behave during processing. Polymers with a high MFI are easier to mold and extrude, making them suitable for applications like injection molding, blow molding, and film extrusion. Materials with a low MFI, however, are more resistant to flow and may be better suited for applications requiring greater strength or durability, such as structural components in automotive or industrial applications.
- Ensuring Consistency in Production
Maintaining consistent material properties is critical to achieving uniform product quality. Variations in MFI between polymer batches can lead to discrepancies in how the final product performs, potentially affecting its appearance, strength, and other mechanical properties. Regular MFI testing helps ensure that each batch of polymer behaves consistently, reducing the risk of defects and improving the overall reliability of the production process.
- Optimizing Polymer Formulations
MFI testing is an essential tool in the development and optimization of polymer formulations. By adjusting the composition of a polymer blend, manufacturers can modify its MFI value to suit specific processing requirements or enhance certain material properties. This capability is particularly important for creating customized polymers that meet the specific needs of industries such as packaging, automotive, and medical devices.
- Compliance with Industry Standards
Many industries have strict regulatory standards that materials must meet to ensure safety, performance, and reliability. Melt Flow Index Testing helps manufacturers confirm that their polymer materials comply with industry standards and regulatory requirements. This is especially important in sectors such as food packaging, medical products, and automotive manufacturing, where material consistency and performance are critical.
How Does a Melt Flow Index Tester Work?
A Melt Flow Index Tester is a specialized piece of equipment used to measure the MFI of polymers. The process is relatively straightforward:
- Heating: A polymer sample is placed in a barrel, which is heated to the polymer’s melting point. The temperature is carefully controlled to ensure the material melts uniformly.
- Flowing Through the Die: Once the polymer has melted, it is forced through a small die opening under a predetermined weight or pressure. The size of the die can vary depending on the test specifications.
- Measuring the Flow: The amount of polymer that flows through the die is measured over a set time (typically 10 minutes). The result is recorded in grams per 10 minutes (g/10min), which provides the MFI value.
This test provides valuable information about the flow characteristics of a polymer, which directly impacts its suitability for various manufacturing processes.
Applications of MFI Testing
- Polymer Production
MFI testing is a crucial step in ensuring that polymer resins are consistent and suitable for the desired end application. Whether producing polyethylene, polypropylene, or any other thermoplastic, understanding the MFI helps manufacturers achieve consistent product characteristics and optimize production processes.
- Plastic Processing
In industries such as injection molding, extrusion, and blow molding, MFI testing is used to assess how a polymer will behave during these processes. The MFI value helps manufacturers adjust processing conditions, such as temperature and pressure, to optimize production efficiency and ensure high-quality finished products.
- Automotive Industry
The automotive industry relies on a variety of polymer-based components, ranging from interior parts to under-the-hood applications. Melt Flow Index Tester Price helps ensure that the polymers used in automotive parts meet the required flow properties and performance standards. This testing also ensures that the materials are suitable for mass production and consistent in quality.
- Packaging
In the packaging industry, polymers are used to produce films, bottles, and other containers. MFI testing ensures that the materials flow properly during production, leading to consistent and high-quality packaging products. The ability to control the MFI helps manufacturers meet both production demands and regulatory requirements.
Benefits of Using Pacorr’s Melt Flow Index Tester
- Accuracy and Reliability
At Pacorr, our Melt Flow Index Testers are designed to deliver highly accurate and reliable results. This ensures that manufacturers can trust the data they collect to make informed decisions about their production processes and product quality.
- User-Friendly Operation
Our Melt Flow Index Testers are equipped with an intuitive interface that makes it easy for operators to conduct tests quickly and efficiently. The straightforward design minimizes the need for extensive training, allowing manufacturers to focus on improving production without unnecessary downtime.
- Durability and Longevity
Built with high-quality materials, Pacorr’s Melt Flow Index Testers are durable and built to last, even in high-volume production environments. The robust construction ensures long-term performance, providing manufacturers with reliable results for years to come.
- Cost-Effective Quality Control
Investing in a Melt Flow Teste from Pacorr provides a cost-effective solution for maintaining high standards of quality control. By regularly testing the MFI, manufacturers can optimize their processes, reduce waste, and improve overall production efficiency.
Conclusion
The Melt Flow Index Tester is an indispensable tool for polymer manufacturers looking to optimize their production processes, maintain product consistency, and meet regulatory standards. At Pacorr, we provide high-quality testing instruments that ensure accurate, reliable results every time. By investing in a Melt Flow Index Tester, manufacturers can gain valuable insights into the flow properties of their materials, enabling them to achieve better product quality and efficiency in their operations.
What's Your Reaction?
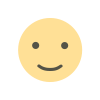

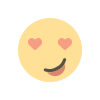

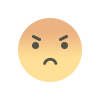

