Comprehensive Guide to the Salt Spray Test Procedure
The salt spray test is a vital tool for manufacturers across various industries. It provides an accelerated insight into how materials and coatings will hold up against corrosion in real-world environments.
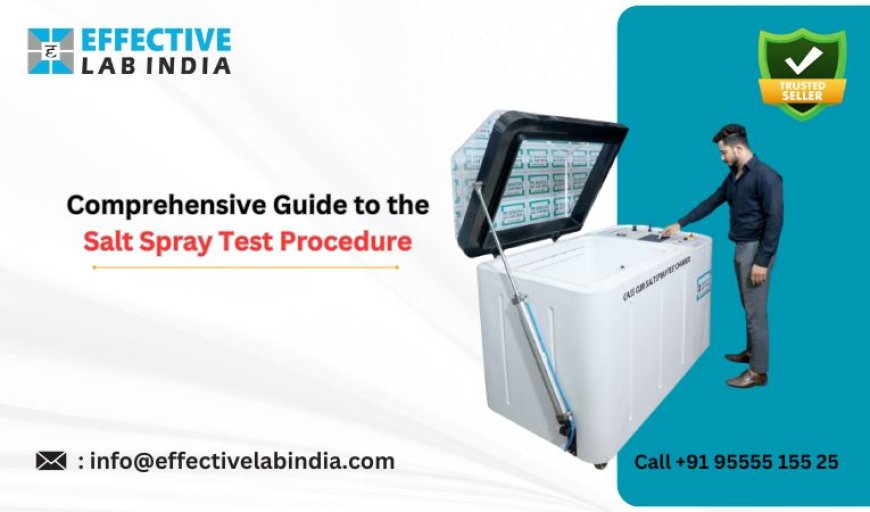
When it comes to ensuring the durability of metal products and components, corrosion testing plays a pivotal role. One of the most widely used methods for corrosion testing is the Salt Spray Test. This test helps manufacturers understand how resistant their products are to corrosion, making it essential in industries like automotive, aerospace, construction, and electronics.
What is the Salt Spray Test?
Let's first define the salt spray test so that we can learn more about it in depth.
An instrument called salt spray chamber that is used to simulates a corrosive environment is the salt spray test, often called the salt fog test. In the test, a steady, regulated salt mist is applied to materials (such as metals and coatings). This environment is a good example of extreme weather, particularly in industrial or marine regions where high air salt concentrations can accelerate corrosion.
The test's principle is straightforward: a material or coating has a greater chance of surviving longer in actual circumstances if it can endure a highly corrosive environment for an extended duration of time.
Why is the Salt Spray Test Important?
For industries that rely on metal components, corrosion can lead to failure, safety issues, and costly repairs. Consider vehicles, bridges, ships, or metal tools exposed to the elements. Corrosion can weaken these structures over time, making them unsafe or unusable.
The salt spray test is an accelerated corrosion test, which means it helps predict how a material will behave over years of exposure in a shorter time frame often in a matter of days or weeks.
The Salt Spray Test Procedure: Step-by-Step
Now, let’s break down the salt spray test procedure into simple steps.
1. Preparation of the Specimen
The first step in the procedure is preparing the material or product you want to test, called the specimen. Typically, the specimen is a metal part or a coated material like a painted or galvanized surface.
- Cleaning the specimen: Before the test, the specimen needs to be thoroughly cleaned to remove dirt, grease, or any contaminants that could interfere with the results.
- Masking non-test areas: If there are specific parts of the specimen that should not be exposed to the salt spray, they are masked off using a protective coating or tape.
2. Setting Up the Salt Spray Chamber
Next, the specimen is placed inside the salt spray chamber—a sealed cabinet designed to create a controlled corrosive environment.
- Salt solution preparation: The salt spray test uses a 5% sodium chloride (NaCl) solution, which is mixed with distilled water. This salt solution mimics the salty air found in coastal or industrial regions.
- pH balance: The salt solution should have a pH between 6.5 and 7.2. This range is critical because it ensures the salt fog will mimic natural sea spray, which is slightly neutral in pH.
The salt spray chamber continuously sprays the salt solution as a fine mist (or fog) throughout the test, ensuring that the specimen is constantly exposed to the salt-laden air.
3. Starting the Test
Once the specimen is securely inside the chamber and the solution is ready, the actual testing begins.
- Test duration: The test can run for hours, days, or even weeks, depending on the product being tested and the industry standards. Common test durations include 24, 48, 72, or 96 hours.
- Test conditions: The chamber operates at a temperature of around 35°C (95°F), maintaining a humid and corrosive environment. The salt fog continuously fills the chamber, simulating the effect of saltwater exposure on the specimen.
4. Monitoring the Test
During the test, technicians periodically monitor the chamber and the specimen to ensure the equipment functions properly.
Some factors checked during the test include:
- Chamber temperature
- Salt solution levels
- pH of the salt solution
5. Test Completion and Inspection
Once the test is finished, it’s time to inspect the specimen.
- Rinse the specimen: After removing the specimen from the chamber, it’s rinsed with clean water to remove any salt residue from the surface.
- Visual inspection: The first step in the inspection is a visual check for signs of corrosion, such as rust spots, blistering, or discolouration.
- Quantitative assessment: Depending on the test requirements, a more detailed analysis may follow, such as measuring the depth of corrosion or the area affected.
6. Documentation of Results
After the inspection, the results of the test are documented. The findings will depend on the industry standard or specific test goals. Common documentation includes:
- Amount of corrosion: The percentage of the surface that shows visible corrosion.
- Time to failure: How long the specimen lasted in the chamber before showing signs of corrosion.
Factors That Affect Salt Spray Test Results
Several factors can influence the outcome of a salt spray test:
- Coating quality: Well-applied coatings (like paint, powder coating, or galvanization) can protect metals longer during the test.
- Material composition: Different metals corrode at different rates. For example, stainless steel is more resistant to corrosion than regular steel.
- Environmental conditions: Even slight changes in temperature or humidity inside the chamber can affect the rate of corrosion.
Real-World Applications of Salt Spray Testing
Industries that produce products exposed to outdoor conditions or harsh environments widely use the salt spray test:
- Automotive industry: Car manufacturers use the test to ensure that metal parts (such as bolts, frames, and body panels) can withstand years of exposure to road salt and moisture.
- Marine industry: Ships, boats, and other marine equipment constantly face exposed to saltwater, making corrosion resistance critical.
- Construction: Building materials like steel beams or outdoor fixtures must be able to withstand the elements over time.
Conclusion
The salt spray test is a vital tool for manufacturers across various industries. It provides an accelerated insight into how materials and coatings will hold up against corrosion in real-world environments. By following a controlled and repeatable procedure, manufacturers can ensure their products meet high standards of durability and performance.
Understanding the salt spray test and its procedure helps you appreciate the effort that goes into creating corrosion-resistant products, ensuring safety and reliability for years to come. If you're in an industry where corrosion resistance is a priority, this test is a must-have in your quality assurance process.
Feel free to reach out to us for any inquiries or assistance! Call us at +91 9315867417 or send an email to info@effectivelabindia.com. Our team is ready to provide support and answer your
What's Your Reaction?
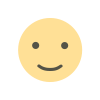

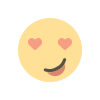

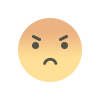

