Efficient Heating Solutions Exploring the Benefits of Heat Tracers and Heating Pads
Explore how heat tracers and heating pads enhance efficiency in various sectors by maintaining temperatures and optimizing energy use effectively.
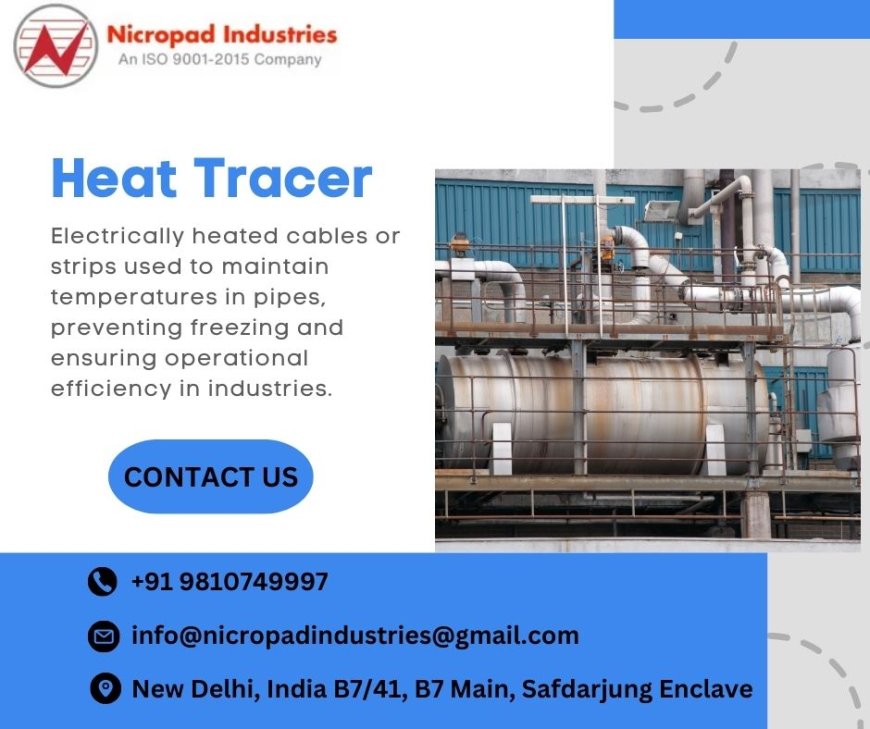
In industrial settings, where maintaining ideal temperatures is essential for operations, effective heating solutions are essential. Two essential technologies that provide focused heating solutions are heat tracer and heating pads. Heat tracers avoid freezing and maintain constant temperatures, enabling the continued operation of critical pipes and equipment. Conversely, heating pads offer targeted heating solutions for particular uses, such as home heating requirements or industrial activities. This article analyzes how these technologies support increased productivity, cost savings, and operational efficiency across a range of industrial industries.
Understanding Heat Tracers
Heat tracers are wires or strips that are heated electrically and used to apply heat directly to objects like tanks, pipes, and instruments. In industrial situations, they are essential to preventing freezing, maintaining process temperatures, and guaranteeing the density of fluids. Multiple types of heat tracers, such as self-regulating and constant energy, are available to meet diverse climatic situations and temperature control requirements. Gaining an understanding of the fundamentals of heat tracer operation is essential to maximizing their efficiency and guaranteeing dependable operation in a variety of industrial applications.
Applications of Heat Tracers in Industrial Settings
Heat tracers have been used in many different industries for a range of purposes. They keep pipelines from freezing in the oil and gas industries and preserve the uniformity of the flow of fluid in dry areas. Heat tracers are used in chemical processing to make sure that materials are kept at the right temperature for effective reactions and processing. Heat tracers are used in the food processing industries to prevent the development of bacteria in pipes that convey sensitive food components, hence maintaining hygiene. These uses highlight the adaptability and crucial function of heat tracers in improving operational dependability and effectiveness in industrial settings.
Benefits of Heat Tracers in Preventing Freezing
The capacity of heat tracers to keep pipelines, tanks, and other equipment sensitive to cold temperatures from freezing is their main advantage. Heat tracers prevent costly downtime caused by frozen systems and guarantee ongoing operations by maintaining consistent temperatures. This dependability is especially important in sectors like oil and gas, where frozen pipelines can cause production delays and safety risks. These sectors place a high value on process continuity. By lowering the possibility of damage from freezing and subsequent melting cycles, heat tracers also help equipment last longer, increasing overall operational efficiency and lowering maintenance costs.
Types and Features of Heating Pads
For targeted heating applications, heating pads are flexible electrically heated devices. They can be found in a variety of forms, such as flexible foil heaters, heated blankets, and silicone rubber mats. Features like uniform heat distribution, temperature adjustments, and durability make heating pads ideal for a variety of industrial applications. Because of these characteristics, they are versatile options for regulating temperatures in tanks, machinery, and specialized processes where exact heat management is required.
Industrial Applications of Heating Pads
Heating pads are used in industrial settings for a variety of purposes, including process heating, material curing, and tank and equipment temperature maintenance. They are employed in the production of electronics, textiles, and polymers, where accurate temperature control is crucial to both efficiency and quality. In the auto, aerospace, and medical sectors, heating pads are also used for a variety of purposes, from composite bonding to preserving pharmaceutical storage temperatures. They are crucial tools for increasing production and preserving operational reliability in a variety of industrial sectors due to their adaptability and efficacy.
Efficiency Comparison Heat Tracers vs. Heating Pads
Depending on the needs of the application, heat tracers and heating pads each have special advantages. In order avoid freezing and guarantee continued operation, heat tracers are excellent at maintaining constant temperatures along pipelines and equipment surfaces. In contrast, heating pads offer targeted heating and are adaptable for uses needing precision temperature regulation in particular regions. Both technologies add to the overall effectiveness and cost-effectiveness of industrial heating solutions however, the decision between heat tracers and heating pads depends frequently on elements like the needed heating scale, environmental variables, and operational goals.
Energy Savings and Cost Effectiveness
When compared to conventional heating techniques, heat tracers and heating pads both help reduce energy use and costs. These devices optimize energy use and reduce heat loss by directly applying heat to surfaces or specific locations. By keeping temperatures continuous without overheating or underheating, heat tracers minimize energy waste and lessen the running costs of heating systems. By providing localized heating solutions, heating pads reduce the need to unnecessarily heat large spaces. All things considered, these energy-saving techniques not only cut utility expenses but also help achieve sustainability objectives by reducing the carbon footprints left by industrial heating activities.
Installation Considerations for Industrial Settings
To maximize their efficiency and guarantee safety in industrial settings, heat tracers and heating pads must be installed correctly. Choosing a suitable tracer or pad type and size according on the environment and heating requirements is one installation consideration. For dependable operation in a range of temperatures and to stop heat loss, proper waterproofing and insulation are required. Furthermore, following industry and manufacturer installation recommendations reduces the danger of electrical risks and breakdowns in equipment, guaranteeing long-term operating reliability and safety.
Safety Measures and Compliance
In order to avoid electrical risks, fires, and equipment damage, safety is essential while using heat tracers and heating pads in industrial environments. Attention to safety protocols and guidelines is crucial during installation, operation, and maintenance to guarantee occupational safety and prevent accidents. A few examples of safety precautions are routine inspections, appropriate insulation, grounding electrical components, and staff training on safe handling techniques. Businesses may reduce the risks connected to heating technologies and establish safer work environments that support operational efficiency and productivity by putting a high priority on safety and compliance.
Conclusion
In industrial settings, efficient heating solutions such as heat tracers and heating pads are crucial because they offer targeted heating solutions that guarantee cost-effectiveness, operational reliability, and productivity. Heat tracers save downtime and maintenance costs by minimizing freezing and maintaining constant temperatures along pipelines and equipment. Heating pads provide flexible uses for targeted heating requirements, boosting productivity in a range of industrial operations. By optimizing heat dispersion and lowering total energy use, both methods support sustainable and energy savings. Industries can optimize the advantages of these heating solutions while producing safer and more productive work environments by following correct installation procedures, safety precautions, and regulatory compliance. As we move forward, technological developments will likely lead to even bigger improvements in sustainability and efficiency for industrial heating applications.
What's Your Reaction?
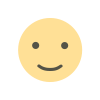

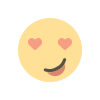

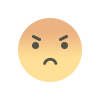

