Ultimate Guide to Circuit Breaker Maintenance in Industrial Settings
Circuit breakers are essential in industrial electrical systems, offering protection by interrupting current flow in case of faults, overloads, or short circuits. Proper circuit breaker maintenance in industrial settings ensures operational reliability, safety, and longevity of electrical systems. This guide provides an in-depth look at maintenance practices for circuit breakers to help industries maximize performance and minimize risks.
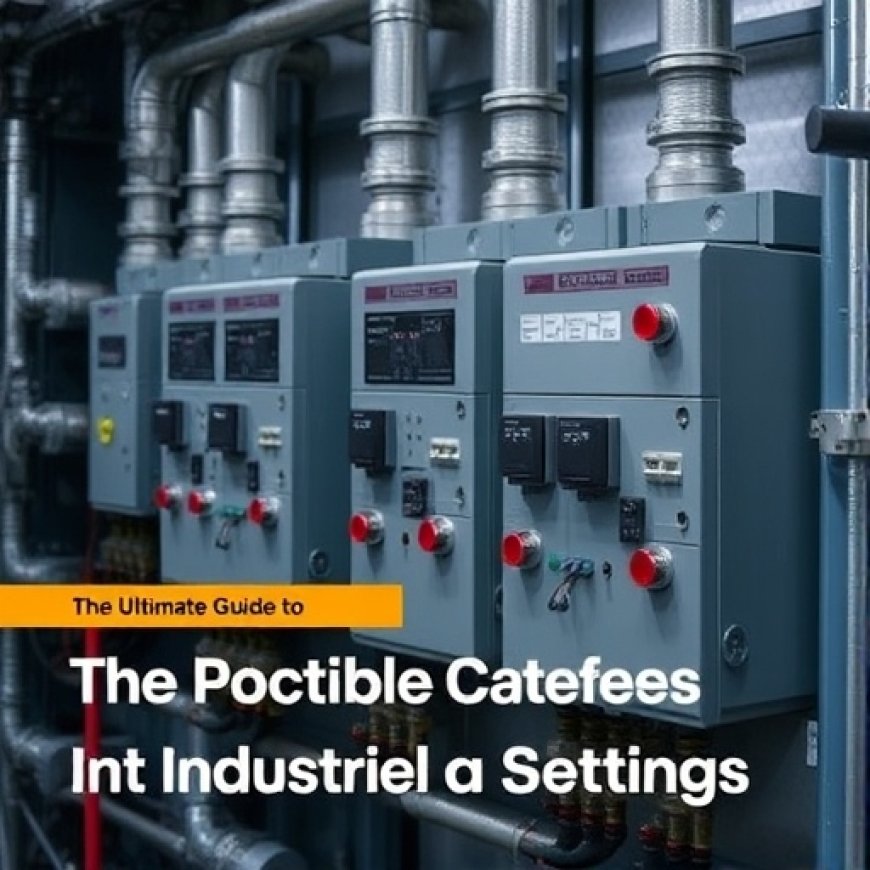
Why Circuit Breaker Maintenance is Critical in Industrial Settings
1. Enhanced Safety: Circuit breakers protect equipment and personnel from electrical hazards. Proper maintenance ensures they function reliably, reducing risks of electric shock, fires, and arc flashes.
2. Reduced Downtime: Unexpected circuit breaker failures can lead to costly unplanned shutdowns. Regular maintenance helps prevent these failures, keeping production lines and processes running smoothly.
3. Cost Savings: Repairing or replacing circuit breakers due to poor maintenance is expensive. Routine checks and repairs can extend the equipment's life and save on costly replacements.
4. Regulatory Compliance: Many industries must meet electrical safety standards. Maintaining circuit breakers helps meet regulatory requirements and avoid penalties.
Types of Circuit Breakers in Industrial Settings
Understanding the types of circuit breakers used in industrial settings is the first step toward effective maintenance. Common types include:
- Air Circuit Breakers (ACBs): Used for low-voltage applications; require contact and insulation checks due to exposure to dust and moisture.
- Vacuum Circuit Breakers (VCBs): Suitable for medium-voltage applications; need vacuum integrity tests and contact assessments.
- SF6 Circuit Breakers: Used in high-voltage applications with SF6 gas as an insulating medium; require gas analysis and refilling if necessary.
- Molded Case Circuit Breakers (MCCBs): Protect lower-voltage circuits; often used in distribution panels and require occasional visual inspections.
Key Maintenance Practices for Circuit Breakers
1. Visual Inspection
- Purpose: Identify obvious signs of wear, overheating, corrosion, or damage.
- Steps: Inspect the breaker’s exterior for discoloration, cracks, or residue buildup. Regular visual checks prevent further deterioration and reveal potential issues early.
2. Contact Resistance Testing
- Purpose: Ensure low resistance between contacts for efficient current flow.
- Steps: Use a micro-ohmmeter to test the contact resistance. Higher-than-normal resistance indicates contact wear, oxidation, or contamination that should be addressed promptly.
3. Insulation Resistance Testing
- Purpose: Ensure proper insulation to prevent electrical leaks or shorts.
- Steps: Using an insulation tester, measure resistance between the breaker’s components. Low insulation resistance indicates degraded insulation, which could cause faults.
4. Mechanical Operation Testing
- Purpose: Confirm the breaker's ability to open and close smoothly and within designated times.
- Steps: Test the breaker's closing and tripping times with a breaker analyzer. Adjust springs, linkages, or dampers if delays or irregularities are observed.
5. Thermal Imaging
- Purpose: Identify hotspots that indicate excessive heat buildup due to poor connections or worn components.
- Steps: Use an infrared thermal camera to inspect the breaker for abnormal heat patterns. Immediate repair or replacement of overheated parts helps prevent failures.
6. Gas Analysis for SF6 Circuit Breakers
- Purpose: Maintain proper gas quality and pressure in SF6 breakers to ensure effective insulation and arc-quenching.
- Steps: Use a gas analyzer to check SF6 purity and pressure. Refill or condition gas if readings fall outside recommended levels.
7. Partial Discharge Testing
- Purpose: Detect early insulation degradation in high-voltage breakers.
- Steps: Conduct partial discharge testing to locate potential weak spots in insulation. Addressing these issues early helps avoid complete insulation failure.
8. Trip Unit Calibration
- Purpose: Ensure the breaker responds accurately to fault conditions.
- Steps: Use specialized test equipment to calibrate the trip unit, checking that it meets the system’s fault response requirements. Correct any misalignments in tripping thresholds.
9. Lubrication of Moving Parts
- Purpose: Prevent friction-induced wear and ensure smooth operation.
- Steps: Regularly apply recommended lubricants to all moving parts, including hinges, springs, and linkages. Avoid over-lubrication, which can attract dust and cause sticking.
Creating a Maintenance Schedule for Circuit Breakers
Developing a consistent maintenance schedule is essential for effective circuit breaker upkeep. Here’s a suggested approach:
- Monthly Checks: Perform visual inspections, thermal imaging, and contact assessments to identify any immediate issues.
- Quarterly Tests: Conduct mechanical operation tests, insulation resistance testing, and partial discharge testing for high-voltage breakers.
- Annual Maintenance: Perform gas analysis for SF6 breakers, trip unit calibration, and detailed cleaning and lubrication.
- Post-Fault Assessment: Any time a breaker trips due to a fault, perform a full inspection to verify it’s still operating within specifications.
Common Signs of Circuit Breaker Issues
It’s essential to recognize early warning signs that a circuit breaker needs attention:
- Frequent Tripping: Indicates an overloaded circuit, incorrect settings, or a malfunctioning trip unit.
- Visible Wear or Damage: Discoloration, cracks, or residue buildup can signal overheating or corrosion.
- Burning Smell or Sounds: Smells or abnormal sounds like buzzing or humming can indicate electrical arcing or loose connections.
- Unusual Heating: A sign of poor connections, damaged contacts, or excessive load, often detected through thermal imaging.
Advanced Monitoring and Predictive Maintenance
Modern industrial facilities are increasingly using advanced monitoring solutions to manage circuit breaker maintenance effectively. By implementing real-time data collection and predictive analytics, companies can proactively address potential issues before they impact operations.
- Remote Monitoring Systems: These systems collect data on breaker status, operating times, and fault history. This information allows maintenance teams to detect abnormalities early.
- Predictive Analytics Software: Software tools analyze breaker data trends to identify components at risk of failure, facilitating a shift from reactive to proactive maintenance.
Conclusion
Circuit breaker maintenance is a cornerstone of electrical safety and operational efficiency in industrial settings. Through consistent inspections, tests, and proactive measures, industries can extend circuit breaker life, avoid unexpected shutdowns, and create a safer work environment. By implementing a structured maintenance program and leveraging advanced monitoring technologies, industries can maintain seamless operations and ensure their electrical infrastructure remains reliable and secure.
Proactive Measures: The Impact of Diagnostic Testing on Generator Longevity
What's Your Reaction?
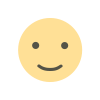

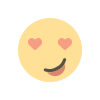

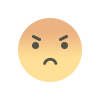

