Versatile Solutions: Exploring the Benefits and Uses of Vacuum Form Plastic Sheets

Plastic has become a cornerstone material in the manufacturing and packaging industries due to its versatility, durability, and affordability. Among the many forms of plastic used today, vacuum form plastic sheets stand out for their adaptability and wide range of applications. These sheets, produced using vacuum forming techniques, offer numerous advantages and are commonly utilized in industries such as automotive, packaging, healthcare, and retail. In this article, we will explore the benefits, uses, and importance of Vacuform plastic sheets, as well as provide insights into finding reliable vacuum forming plastic sheet suppliers.
What Are Vacuum Form Plastic Sheets?
Vacuum form plastic sheets are thermoplastic materials that are heated to a pliable temperature and then shaped over a mold using vacuum pressure. This process ensures precise shaping and consistent results, making it ideal for creating customized designs and components. The sheets come in a variety of thicknesses, colors, and textures, catering to the diverse needs of different industries. Common thermoplastics used in vacuum forming include acrylic, polycarbonate, ABS (Acrylonitrile Butadiene Styrene), and PETG (Polyethylene Terephthalate Glycol).
The versatility of these sheets allows manufacturers to produce items with intricate designs, smooth finishes, and robust durability—all at an affordable cost. Whether it’s for producing trays, enclosures, packaging materials, or signage, vacuum form plastic sheets offer a practical solution.
Benefits of Vacuum Form Plastic Sheets
-
Cost-Effectiveness Vacuum form plastic sheets are an economical choice for both small and large-scale projects. The vacuum forming process requires minimal tooling compared to other methods like injection molding, which can significantly reduce production costs.
-
Lightweight and Durable These sheets are lightweight yet incredibly durable, making them suitable for a variety of applications. Their strength-to-weight ratio ensures that they can withstand impact, resist wear and tear, and maintain structural integrity over time.
-
Customizability One of the major advantages of vacuform plastic sheets is their customizability. They can be tailored to meet specific design requirements, including size, shape, color, and texture. This makes them ideal for industries requiring unique or branded solutions.
-
Eco-Friendly Options With increasing emphasis on sustainability, Vacuum forming plastic sheet suppliers now offer eco-friendly options made from recyclable or biodegradable materials. These options help reduce environmental impact while maintaining the benefits of traditional plastic sheets.
-
Ease of Manufacturing The vacuum forming process is straightforward and efficient, enabling quick turnaround times for high-quality products. This ensures manufacturers can meet tight deadlines without compromising on quality.
Uses of Vacuum Form Plastic Sheet
-
Automotive Industry Vacuum form plastic sheets are extensively used in the automotive sector for producing interior and exterior components such as dashboards, door panels, bumpers, and protective covers. Their lightweight nature helps improve fuel efficiency, while their durability ensures longevity.
-
Packaging These sheets are ideal for creating custom packaging solutions, including blister packs, clamshells, and trays. The ability to mold them into specific shapes ensures secure packaging for delicate or irregularly shaped items.
-
Healthcare In the healthcare industry, vacuform plastic sheets are used for creating medical device enclosures, trays, and packaging for surgical instruments. Their hygienic properties, along with the ability to withstand sterilization processes, make them an essential material in this field.
-
Retail and Point-of-Sale Displays Retailers utilize these sheets for eye-catching signage, displays, and product stands. Their versatility allows for creative designs that can effectively attract customers and showcase products.
-
Construction and Architecture Vacuum form plastic sheets are used in architectural applications such as decorative panels, lighting diffusers, and wall cladding. Their ability to mimic textures like wood or metal adds aesthetic value while maintaining affordability.
-
Aerospace Industry In aerospace, these sheets are employed for producing lightweight and durable components, including storage compartments and seatbacks. Their high-performance qualities ensure they meet the stringent safety and durability standards of this industry.
Choosing Reliable Vacuum Forming Plastic Sheet
Finding the right supplier is crucial to ensuring high-quality products and reliable service. When selecting vacuum forming plastic sheet suppliers, consider the following factors:
-
Material Quality Ensure the supplier offers premium-quality plastic sheets that meet industry standards. The material should be durable, consistent, and suitable for your specific application.
-
Customization Options A good supplier should provide extensive customization options to meet your design and production requirements. This includes offering a range of thicknesses, colors, and textures.
-
Lead Times Timely delivery is essential for maintaining smooth production processes. Choose suppliers with a track record of meeting deadlines and providing efficient service.
-
Sustainability Practices If sustainability is a priority for your business, opt for suppliers that offer eco-friendly materials and adhere to environmentally responsible manufacturing practices.
-
Technical Support A reliable supplier will provide technical support and guidance to ensure you choose the right material and specifications for your project.
Conclusion
Vacuum form plastic sheets are a versatile and cost-effective solution for a wide range of industries. Their adaptability, durability, and customizability make them indispensable in applications ranging from automotive parts to retail displays. By choosing reliable vacuum forming plastic sheet suppliers, businesses can ensure they receive high-quality materials that meet their specific needs. As industries continue to evolve, the demand for innovative and sustainable plastic solutions will only grow, further solidifying the importance of vacuform plastic sheets in modern manufacturing.
Frequently Asked Questions (FAQs)
1. What materials are commonly used for vacuum form plastic sheets? Vacuum form plastic sheets are typically made from thermoplastics such as acrylic, polycarbonate, ABS, and PETG. Each material offers unique properties, such as impact resistance, clarity, or flexibility, making them suitable for different applications.
2. Are vacuum form plastic sheets environmentally friendly? Many suppliers now offer eco-friendly options, including sheets made from recyclable or biodegradable materials. Choosing such options can help reduce the environmental impact of plastic products.
3. How can I find the right vacuum forming plastic sheet supplier? Look for suppliers that offer high-quality materials, extensive customization options, and reliable delivery. Additionally, prioritize suppliers with a commitment to sustainability and excellent customer support.
What's Your Reaction?
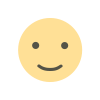

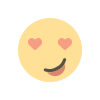

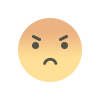

