Why Closed-Cell Foam Is Ideal for Large Commercial Roofs
In this article, we explore why closed-cell spray foam is often the smartest choice for commercial roofing projects.
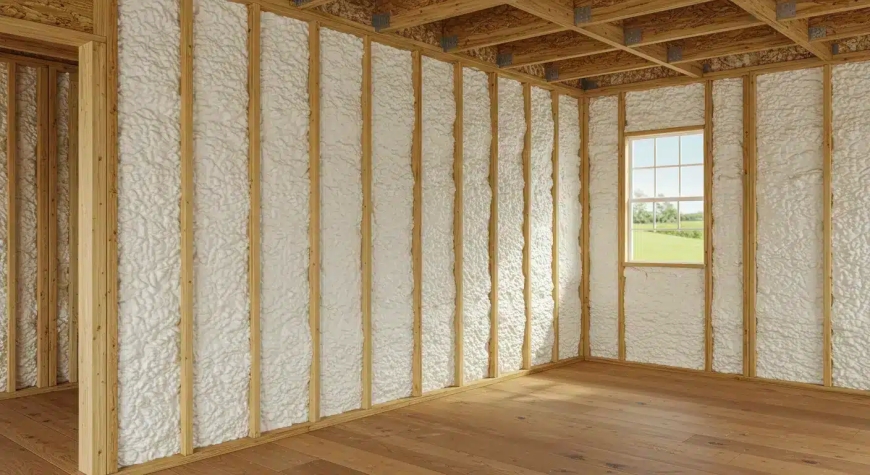
Closed-cell spray foam has emerged as one of the most effective insulation and roofing materials for large-scale commercial properties. Offering superior durability, a high R-value, and inherent moisture resistance, this material has become a go-to solution for flat and low-slope commercial roofs. Its seamless application, coupled with long-term performance benefits, makes it particularly suitable for facilities that demand year-round operational efficiency and minimal maintenance interruptions.
In this article, we explore why closed-cell spray foam is often the smartest choice for commercial roofing projects. We’ll examine its benefits, technical specifications, comparison with other insulation types, real-world adoption trends, and what decision-makers should consider before installation.
Why Closed-Cell Spray Foam Stands Out for Commercial Roofing
Closed-cell spray polyurethane foam (SPF) combines high-performance insulation with reliable waterproofing in a single applied system. Unlike conventional roofing systems, which often require multiple layers for insulation, air sealing, and water resistance, closed-cell foam delivers all three in one continuous, monolithic layer. This means fewer seams, reduced risk of water intrusion, and enhanced structural stability.
Key advantages include:
-
R-value between 6.0–7.0 per inch for superior thermal resistance
-
Reinforcement of roof decking through rigid foam strength
-
Minimal water absorption (<2%), making it ideal for humid regions
-
Broad adhesion compatibility with existing substrates, allowing retrofits
-
Seamless barrier reduces maintenance needs and long-term repair costs
Bonus Tip: Closed-cell foam creates a high-density surface that resists hail damage and impact from debris, which is especially beneficial in storm-prone areas.
Understanding Closed-Cell Foam vs. Other Insulation Types
While there are several commercial roofing insulation options, few offer the all-around performance of closed-cell foam. The table below highlights how it compares to common alternatives.
Comparison Table: Insulation Options for Commercial Roofs
Feature |
Closed-Cell Spray Foam |
Open-Cell Foam |
Rigid Foam Board |
Built-Up Roofing |
R-Value per inch |
6.0–7.0 |
3.5–4.0 |
4.5–5.0 |
2.0–3.0 |
Waterproof |
Yes |
No |
Partial |
Yes |
Structural Support |
High |
Low |
Moderate |
Low |
Air Barrier |
Yes |
Yes |
No |
No |
Seamless Application |
Yes |
Yes |
No |
No |
Best for Large Roofs? |
Yes |
No |
Moderate |
Moderate |
Technical Specifications of Closed-Cell Foam for Roofing
Understanding the physical and performance attributes of closed-cell foam helps in project planning and regulatory compliance. Below are typical values used across commercial roofing systems.
Specification |
Typical Range |
R-Value |
6.0–7.0 per inch |
Compressive Strength |
25–60 psi |
Density |
2.0 lbs/ft³ |
Water Absorption |
<2% |
Application Thickness |
1–3 inches (per pass) |
Bonus Tip: Multiple passes of spray foam can be layered to meet both thermal codes and slope correction needs simultaneously.
Key Advantages in Commercial Settings
Energy Efficiency & Interior Climate Control
Closed-cell foam creates a continuous insulation layer that minimizes heat transfer. This leads to stabilized indoor temperatures, especially valuable for data centers, warehouses, and retail spaces. By reducing HVAC runtime, facilities often experience lower utility bills.
Structural Integrity & Load Support
Its high compressive strength makes closed-cell foam an asset on roofs housing solar panels, HVAC units, or walkways. The foam adds rigidity to the structure without significantly increasing weight load.
Moisture and Vapor Barrier
Because of its closed-cell composition, the foam resists moisture absorption and blocks vapor intrusion. This quality is essential for flat roofs that may hold water or experience seasonal freeze-thaw cycles.
Market Insight: Studies show that commercial buildings using spray foam can reduce energy use by up to 20–30%, contributing significantly to meeting ASHRAE standards.
Things to Consider Before Choosing Insulation
Every commercial roofing project is unique, and choosing the right insulation requires a thorough evaluation of several factors:
-
Climate and Precipitation: Closed-cell foam performs well in wet, humid, or snowy environments due to its moisture resistance.
-
Rooftop Activity: Roofs supporting equipment or maintenance personnel benefit from the material’s high compressive strength.
-
Code Compliance: Local building codes may dictate insulation minimums, fire ratings, or environmental requirements.
-
Retrofit Compatibility: The ability to apply foam over existing roofing systems can reduce project time and disposal costs.
-
Incentives: Programs like the EPA’s ENERGY STAR or state-specific rebate schemes can offset initial investment costs.
Bonus Tip: Before application, assess the roof deck condition. Closed-cell foam requires a clean, dry, and stable substrate for optimal adhesion.
Common Homeowner and Contractor Questions
-
What is the expected service life of closed-cell foam roofs?
With proper installation and UV-protective coatings, they typically last 20 to 30 years.
-
Can it be applied on top of an old roof?
Yes, provided the existing roof is dry, stable, and compatible with spray foam.
-
Are there any special installation conditions?
Foam must be applied during specific temperature and humidity ranges for optimal curing.
-
Does it need UV protection?
Absolutely. Exposure to sunlight degrades foam, so a topcoat like silicone or elastomeric is essential.
-
Is it fire safe?
When paired with intumescent or thermal barrier coatings, it meets commercial fire safety standards.
Frequently Asked Questions About Home Insulation
Q1: What is the difference between closed-cell and open-cell spray foam?
Closed-cell is denser and waterproof, with a higher R-value, making it ideal for exterior and load-bearing applications.
Q2: How does commercial insulation affect energy bills?
By reducing heat loss and air leakage, insulation improves efficiency and lowers monthly utility costs.
Q3: What maintenance does spray foam roofing require?
Annual inspections and recoating every 10–15 years help maintain integrity and performance.
Q4: Is closed-cell foam sustainable?
Modern variants use environmentally safer blowing agents and offer long-term performance, reducing the need for frequent replacements.
Q5: Can spray foam also reduce noise?
Yes. It absorbs airborne sound to some degree, providing acoustic benefits in busy commercial zones.
Finding the Right Insulation Expertise
When insulating a large commercial roof, long-term performance, structural support, and moisture control should guide your material choice. Closed-cell spray foam offers an all-in-one solution that simplifies installation and enhances building performance.
For commercial and residential property owners evaluating roofing and insulation solutions, Spray Tech Solutions is a provider with experience in this field.
Readers can learn more about Spray Tech Solutions' services:
Company: Spray Tech Solutions
Phone: (765) 553-4636
Email: sales@spraytechkokomo.com
Explore their commercial insulation and roofing expertise
What's Your Reaction?
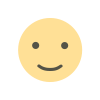

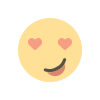

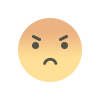

