Corrosion Monitoring Market: Safeguarding Infrastructure Integrity
The global corrosion monitoring market size was valued at USD 388.08 million in 2024 and is expected to reach USD 887.93 million by 2032, at a CAGR of 10.9% during the forecast period
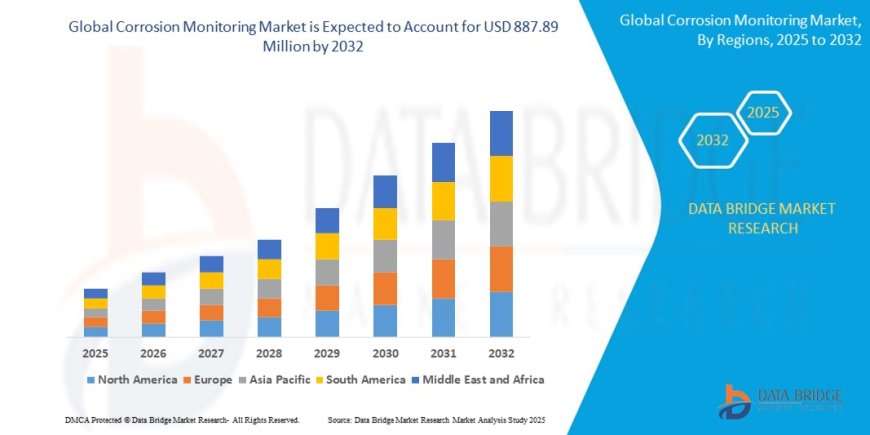
Introduction
The Corrosion Monitoring Market is rapidly becoming a cornerstone of industrial resilience and sustainability. Corrosion—the gradual degradation of materials, especially metals—threatens the safety, performance, and operational efficiency of infrastructure assets across countless sectors. It silently undermines storage tanks, pipelines, bridges, marine structures, chemical reactors, and energy systems, often leading to catastrophic failures that cost millions in lost productivity and regulatory penalties.
As industries grow more asset-intensive and interconnected, companies are transitioning from reactive inspection models to proactive, technology-driven monitoring solutions. These systems integrate predictive analytics, smart sensors, and real-time diagnostics—not only detecting corrosion early but also enabling strategic maintenance planning, regulatory compliance, and optimized asset longevity.
The Evolution of Corrosion Monitoring Systems
Manual Methods: The Early Days
-
Visual Inspections: Relied on trained personnel to observe rust, cracks, or discoloration.
-
Coupon Testing: Used metal samples placed in corrosive environments and assessed post-retrieval.
Limitation: These methods were low-cost but lacked accuracy and timeliness.
The Rise of Electrochemical Sensors
-
Electrical Resistance (ER) Probes: Measure conductivity loss due to metal thinning.
-
Linear Polarization Resistance (LPR): Calculate corrosion rate using low voltage currents.
Impact: Shifted monitoring from qualitative to quantitative, improving predictability.
Non-Destructive Techniques and Industrial Integration
-
Techniques like Ultrasonic Testing (UT), Eddy Current Analysis, and Magnetic Flux Leakage (MFL) allow defect detection without equipment disassembly.
Application: Ideal for high-risk environments like pipelines, boilers, and tank walls.
Smart and Connected Monitoring Systems
-
IoT-enabled sensors and cloud platforms provide remote, real-time data collection.
-
AI-driven analytics help predict failures and recommend maintenance schedules.
-
Wireless Sensor Networks (WSNs) extend coverage to inaccessible zones (e.g., subsea, underground).
Source : https://www.databridgemarketresearch.com/reports/global-corrosion-monitoring-market
Emerging Market Trends
🔹 Real-Time Monitoring
-
Demand is growing for instant corrosion updates via mobile apps, dashboards, and automated alerts.
🔹 Predictive Maintenance
-
AI-enabled systems shift from scheduled to condition-based maintenance, reducing unnecessary interventions.
🔹 Integration with Digital Twins
-
Digital replicas simulate corrosion over time, aiding in strategic planning and visualization.
🔹 Eco-Conscious Innovation
-
Rise of biodegradable coatings, non-toxic inhibitors, and sustainable treatments.
🔹 Miniaturization and Ruggedization
-
Sensors are getting smaller and more durable, ideal for extreme environments.
🔹 Expansion of SaaS Platforms
-
Growth of cloud-based analytics and reporting for corrosion data—accessible and cost-effective for SMEs.
Key Market Challenges
Challenge | Description |
---|---|
Financial Barriers | High installation and training costs, especially for legacy systems. |
Data Management | Massive volumes of sensor data require advanced filtering and AI. |
Environmental Variables | Corrosive conditions like salinity and humidity complicate monitoring. |
Interoperability | Lack of standards among vendors limits system compatibility. |
Talent Shortage | Expertise in corrosion science and digital tech is in short supply. |
Regulatory Compliance | Increasing oversight from environmental and safety agencies. |
Market Scope and Segmentation
Monitoring Techniques
-
Electrochemical Sensors: ER, LPR, and galvanic probes.
-
Ultrasonic Devices: Non-invasive thickness and integrity assessments.
-
Hydrogen Probes: Crucial for detecting hydrogen embrittlement in steel.
-
Optical Sensors: Laser mapping and microstructural analysis.
-
Wireless Sensor Networks (WSNs): Scalable with minimal infrastructure.
-
Fiber Optic Sensors: Deployed in harsh or remote environments.
Industrial Applications
-
Oil and Gas: Pipelines, refineries, offshore rigs.
-
Chemical Processing: Reactors, tanks, pressure vessels.
-
Power Generation: Boilers, turbines, nuclear plants.
-
Water and Wastewater: Pipelines, desalination, treatment facilities.
-
Marine and Shipping: Hulls, ballast tanks, offshore structures.
-
Construction: Bridges, highways, tunnel rebar.
-
Aerospace & Automotive: Aircraft and vehicle structural components.
Geographical Reach
-
North America: Leading adoption of remote and smart platforms.
-
Europe: Emphasis on sustainability and regulation.
-
Asia-Pacific: Fastest growth due to infrastructure and manufacturing.
-
Middle East & Africa: Expanding energy investments.
-
Latin America: Rising industrialization and mining activities.
Market Size and Growth Drivers
Infrastructure Modernization
-
Aging global infrastructure demands proactive corrosion management.
Risk and Incident Prevention
-
High-profile failures highlight need for reliable detection.
Regulation and Compliance
-
Agencies mandate thorough inspection and documentation.
Sustainability and Green Engineering
-
Monitoring supports eco-friendly asset management.
Energy Sector Expansion
-
Growth of oil, gas, hydrogen, and renewables drives demand.
Digitization in Maintenance
-
Integration with EAM, ERP, and Digital Twins enhances strategic planning.
Conclusion
The Corrosion Monitoring Market is entering a new era of strategic importance. In a climate of industrial complexity, environmental responsibility, and digital transformation, monitoring corrosion is no longer a maintenance task—it is a core competency. From chemical plants to coastal bridges, real-time corrosion data is guiding investment decisions, maintenance schedules, regulatory reporting, and safety protocols.
Advanced monitoring technologies, supported by AI, cloud platforms, and sustainable design principles, are reshaping how infrastructure is protected and maintained. As industries embrace predictive maintenance and digital diagnostics, the demand for intelligent corrosion management will accelerate across sectors and continents.
Moving forward, the convergence of sensor engineering, software intelligence, and proactive inspection will define the future of corrosion protection—transforming it from a hidden hazard into a visible, measurable, and controllable aspect of industrial resilience.
What's Your Reaction?
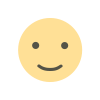

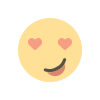

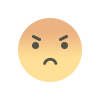

