Avoid Costly Mistakes: How to Source and Install the Right European Packaging Equipment

Choosing the right packaging equipment is one of the most critical decisions for any business involved in manufacturing or distribution.
Yet, many companies fall into costly traps — selecting systems that don’t align with their operations, overpaying for features they don’t need, or struggling with expensive downtime due to poor installation.
If you’re thinking about how to source and install the right European packaging equipment, this guide will walk you through the smart, practical steps to get it right the first time.
European-made equipment is often considered top-of-the-line — but even the best machine won’t deliver results if it’s not matched to your unique needs and properly installed.
Quick Overview: What You Need to Know
-
European packaging equipment offers premium build quality, energy efficiency, and compliance with strict safety standards.
-
The most common sourcing mistakes involve skipping the needs analysis, trusting the wrong suppliers, and overlooking installation planning.
-
Success depends on a structured approach: define your requirements, assess suppliers thoroughly, and treat installation like a project — not an afterthought.
-
Partnering with local experts or agents familiar with European systems can bridge language, logistics, and compliance gaps.
Want to dive deeper and avoid the most expensive missteps? Keep reading.
Step-by-Step: How to Source the Right Equipment
1. Understand Your Packaging Needs (Before You Look at Brochures)
Too many businesses jump into equipment selection without defining their packaging line requirements. Ask yourself:
-
What are the throughput goals per hour or per shift?
-
What type of products and packaging materials are used?
-
Do you need flexibility for different product sizes or future expansion?
-
What are your facility constraints (space, power, climate)?
Pro Tip: Document your current bottlenecks and list the features that would make a meaningful difference in productivity — not just nice-to-haves.
2. Research European Manufacturers and Local Distributors
Europe is home to some of the world’s leading packaging equipment manufacturers — especially in Germany, Italy, and Switzerland. However, not every European brand is the right fit for your business.
Key criteria when evaluating manufacturers:
-
ISO certifications and CE compliance
-
Customisation capabilities
-
Availability of English-language manuals and support
-
Existing installations in your industry
Should you work directly with the European OEM or go through a local supplier?
Going through an experienced local distributor can simplify logistics, customs, and warranty handling. They can also offer training and servicing locally, which is a major plus.
Did You Know? Some Australian and New Zealand-based engineering firms are certified agents for European brands and can coordinate sourcing, shipping, and commissioning end-to-end.
3. Clarify Total Cost of Ownership (TCO)
The sticker price doesn’t tell the whole story. You’ll want to compare the full cost, including:
-
Import duties, freight, and taxes
-
Installation and calibration
-
Ongoing maintenance and spare parts
-
Downtime costs due to lead times for overseas components
Ask for a full breakdown from each supplier and consider their ability to support you after installation.
4. Plan Installation Like a Project (Not a Weekend Job)
Even the best machine can underperform if installation is rushed or poorly executed.
Before delivery:
-
Prep the site (power, space, ventilation, access)
-
Appoint an internal installation team or coordinator
-
Ensure technician availability aligns with equipment arrival
During installation:
-
Insist on proper calibration and performance testing
-
Provide training to operators and maintenance staff
-
Document settings and maintenance schedules
Quote from a packaging expert:
“We see companies spend $150K+ on a great machine, only to have it running at 60% efficiency because no one was trained properly.”
Quick Guide: Common Mistakes & Smarter Solutions
Situation: You’ve Ordered European Equipment… Now What?
You’ve selected the machinery. It’s being shipped from Europe. But now the real work begins — and if you’re not careful, delays and costs can pile up fast.
Common Challenges:
-
Did you assume the supplier handles installation?
-
Are your operators trained on the new interface?
-
Did you check if your facility’s voltage matches European specs?
How to Avoid These Mistakes:
1. Start installation planning early: Begin coordinating site readiness, technician booking, and internal training before the equipment ships.
2. Check compatibility and compliance: Ensure your power supply, safety protocols, and packaging materials all align with the specs of the incoming equipment.
3. Invest in operator training: Arrange for hands-on training during installation or immediately after. Well-trained operators = fewer breakdowns.
4. Document everything: From maintenance schedules to troubleshooting procedures — keep everything in one accessible system.
Why It Works:
Getting ahead of the curve allows you to hit the ground running. You avoid production delays, reduce warranty risks, and extend the lifespan of your investment.
Need help coordinating a smooth installation? Let’s talk.
FAQs About European Packaging Equipment
Q1: Why choose European packaging equipment over cheaper alternatives?
European machines typically offer:
-
Higher build quality and durability
-
Better energy efficiency
-
Advanced automation features
-
Compliance with international safety standards
Long-term, these factors reduce downtime and total operational costs.
Q2: How long does it take to import and install European machinery?
It depends on the country of origin, customs, and equipment complexity. A typical timeline includes:
-
6–10 weeks manufacturing lead time
-
2–4 weeks shipping and customs
-
1–2 weeks installation and calibration
Start early to ensure alignment with your project milestones.
Q3: What’s the biggest risk in buying European equipment?
Lack of after-sales support or miscommunication during installation. Mitigate this by:
-
Working with local reps of European brands
-
Ensuring clear contract terms for support
-
Scheduling post-installation follow-up visits
Q4: Can I modify European equipment to suit my packaging needs?
Yes — most European OEMs offer customisation. Be specific about:
-
Your packaging dimensions
-
Required throughput
-
Any integration with existing systems
Just be aware that modifications can increase lead time and cost.
Q5: What should I look for in a local installer or technician?
Look for:
-
Experience with European brands
-
Electrical and mechanical certifications
-
References from similar projects
Bonus: Choose someone who offers both installation and training.
Conclusion: The Right Machine Is Only Half the Battle
Sourcing European packaging equipment is a smart move — but only if done right. When you take the time to understand your needs, evaluate your options thoroughly, and plan for proper installation and training, you position your business for long-term gains. Avoid the temptation to rush or cut corners.
The real ROI comes from smart sourcing and seamless setup.
Ready to streamline your packaging operations? Start with the right questions — and the right partners.
What's Your Reaction?
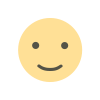

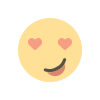

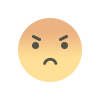

